To be able to prevent and remove workplace hazards is not only needed for employee safety, but it’s also a legal responsibility under the Occupational Safety Health Act’s General Duty Clause requiring employers to provide a safe workplace free of recognized hazards that may cause serious and even fatal injuries to employees.
By implementing strategies that comply with government safety regulations, and taking practical measures relevant to the specific work environment, it’s possible to keep employees protected from many forms of injury. The task of identifying hazards in the workplace and implementing ways to avoid them should always be an ongoing process in companies of all sizes.
This topic deserves attention and therefore below we look at the most common workplace hazards so you can take the appropriate steps and mitigate any unfortunate employee risks.
Chemical Hazards
Workers are often exposed to chemicals in liquids, gases and specific materials. Such chemical hazards include acids, carbon monoxide, flammable liquids, pesticides, and fiberglass. They can make confined spaces very hazardous and damage people’s health by causing skin irritations, eye injuries and blindness, and burns.
Solvents are easily flammable while spray paint cans are prone to exploding and therefore must be labeled accordingly so your employees know when to be extra cautious and always read such labels and follow the directions and precautions precisely.
For instance, if you’re in the industrial manufacturing field, you must be aware of the danger of spills for the workplace and environment. Such spills are unfortunately inevitable and cannot be avoided and require special equipment such as spill containment berms to collect any hazardous spills or leaks, and avoid harmful or toxic substances seeping into the soil or groundwater.
Electrical Hazards
People can be injured by any “live” wires, whether they touch them directly or indirectly through a conducting object or material. Voltages above 50 volts AC are considered hazardous and should not be taken lightly. Electrical shocks can cause severe and permanent injuries. Sadly, many electrical accidents happen at workplaces each year that have a fatal outcome. All this is caused by faulty equipment that should be checked as a preventative measure.
The basic electrical safety steps include maintenance of all electrical installations, choosing the proper equipment for the job, and removing any damaged sections of cables. Also, don’t forget that faulty electrical appliances may also lead to a fire.
Physical Hazards
This might sound like a generic work hazard but it’s an important one to mention. Physical hazards are the most common hazards which happen in the workplace daily and include unguarded machinery, frayed electrical cords, working from ladders, scaffolding or heights.
If you pay close attention during a workday, you will probably come across one or more of these problem areas. Performing job tasks as you’re supposed to without doing foolish stunts will help maintain a safe work environment and ensure employees’ safety. Employers must also ensure that their workers are educated on how to properly operate, move around, and take care of the work equipment.
Ergonomic Hazards
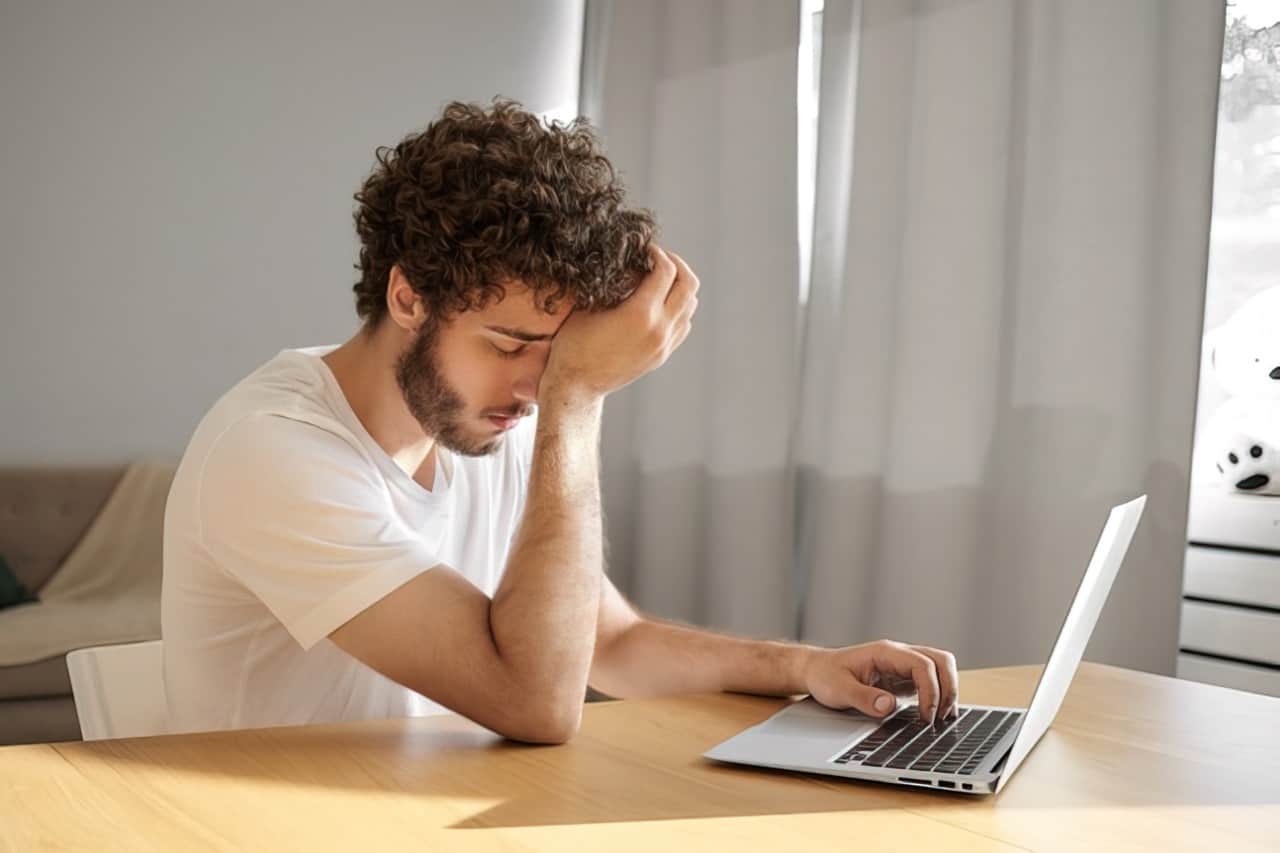
Ergonomics means adapting work to humans to prevent risks of ill health and accidents. When the work you’re doing puts a strain on your body, it can become an ergonomic hazard. It’s very much about how to plan and organize the work and employers are required to see the whole picture. As ergonomic hazards don’t immediately affect employees, they can be tricky to identify but being aware and incorporating ergonomic principles within the workplace can tremendously mitigate hazards and improve efficiency and overall job satisfaction.
Ergonomics includes physical, organizational and mental aspects of the work environment. When making ergonomic improvements in business, they must affect both the employees’ conditions and the technical and organizational conditions.
Even when a business is planned, good ergonomics should permeate the design and interior of the premises and workplaces. To feel good and be able to perform good quality at work, there must be sufficient variation in movement and load and the possibility of recovery.
To organize the work so that it’s good for all employees, it may be necessary to consider whether women and men have the same opportunities for varied workloads and whether there are workers who need special adaptation of the work. The organization of work content, working hours and wage forms also affects the load on the body in both positive and negative ways.
Final Thoughts
Regardless of the industry you work in, minimizing and eliminating workplace hazards should be your main priority. This doesn’t necessarily have to be time-consuming or costly but it’s a matter of planning and organizing the work environment and being aware of the possible hazards ahead of time. By doing so, you’ll be able to increase productivity, prevent illness and injuries, and reduce sickness absence.