Dreaming of a steel home but worried about costs? You’re not alone. Steel homes can cost between $50 to $145 per square foot. This blog will break down the real costs of steel homes.
We’ll share six smart facts to help you save money. Ready to build your dream home without breaking the bank?
Key Takeaways
Steel homes cost between $50 to $145 per square foot, with prefab kits being the cheapest option at $10 to $25 per square foot.
A typical 30×50 steel home (1,500 sq ft) costs $75,000 to $215,000 to build, including materials and labor.
Interior finishing makes up a large part of the cost, ranging from $35 to $110 per square foot for things like painting, cabinets, and HVAC.
Quonset hut homes are often the most affordable steel option, with installed costs of $17 to $34 per square foot.
Steel homes can save up to 50% on utility bills and require much less maintenance than traditional homes, costing only 1% of the initial price annually vs. 2-4% for wood homes.
Table of Contents
Understanding the Costs of Steel Homes
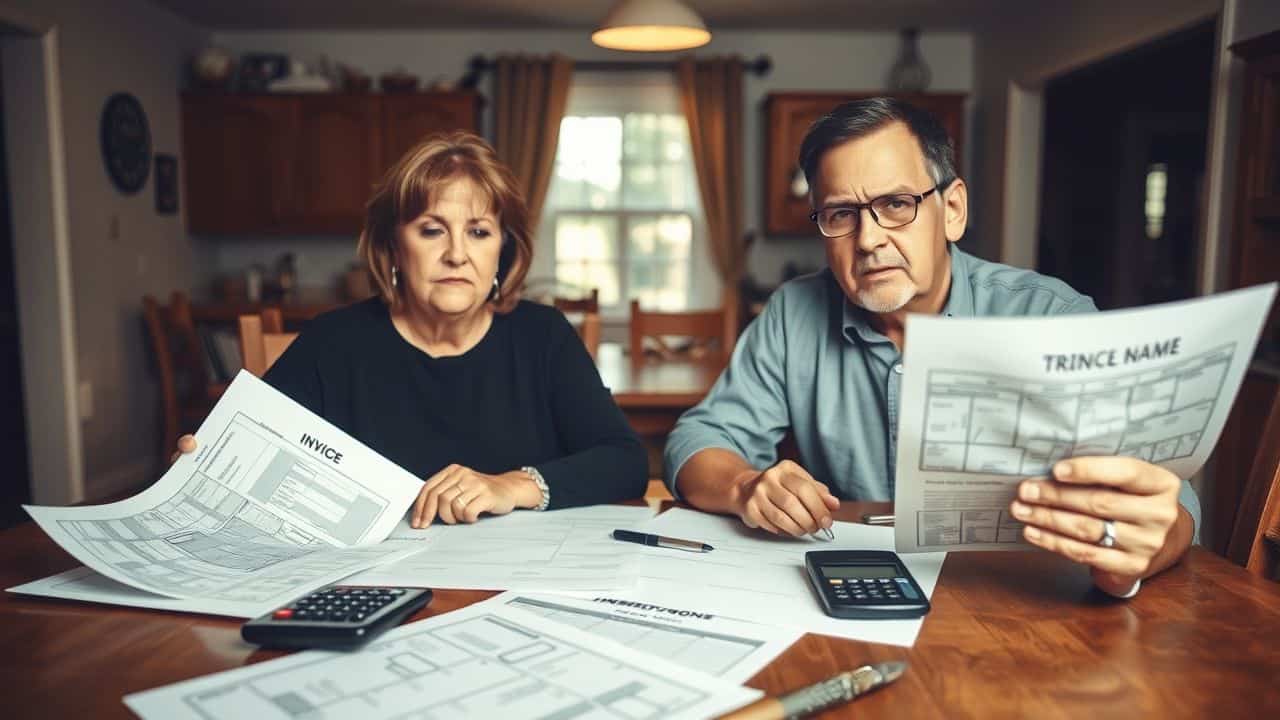
Steel homes can be a real game-changer for your wallet. Let’s break down the numbers and see how much these metal marvels might set you back.
Price Per Square Foot Analysis
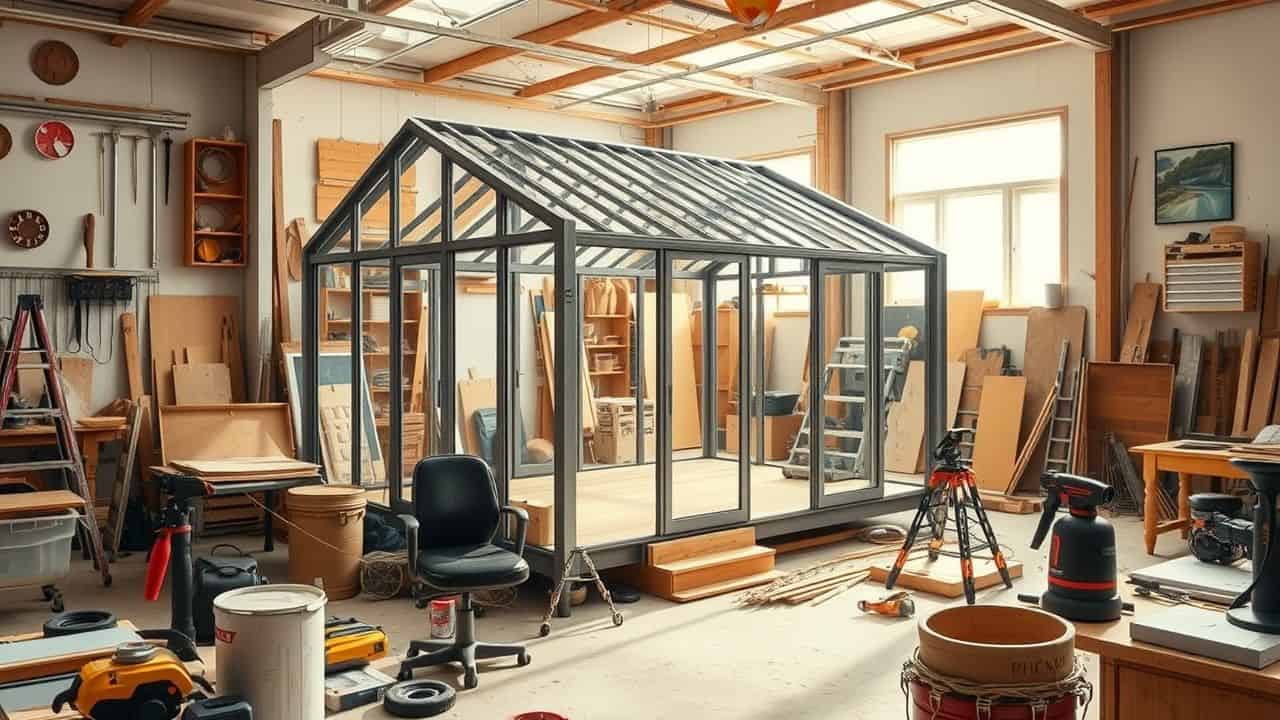
Let’s break down the costs of steel homes. It’s straightforward when you see the numbers. This table gives you a clear idea of the prices you’re looking at.
Type of Steel Home | Price Per Square Foot | Notes |
---|---|---|
Finished Metal Building Home | $50 – $145 | Includes all finishing work |
Prefab Metal House Kit | $10 – $25 | Plans and materials only |
Labor Costs | $5 – $110 | For assembly and finishing |
Prefabricated Metal Building Kit | $15 – $25 | Basic structure |
Now, let’s talk about what these numbers mean. The wide range in prices? That’s because of all the options you’ve got. It’s like picking toppings for a pizza – the more you add, the pricier it gets.
The cheapest route? That’s gonna be the prefab kits. But keep in mind, you’ll need to factor in labor costs if you’re not planning on a DIY project. And trust me, unless you’re a pro, you might want to leave it to the experts.
https://www.youtube.com/watch?v=XIAOsfWilxE
Finished homes cost more upfront, but they’re move-in ready. No fuss, no muss. Just grab your stuff and settle in.
Labor costs can vary a lot. It depends on where you live and how complex your design is. A simple box shape? That’ll be on the lower end. Want something that looks like a modern art museum? Prepare to shell out more.
Here’s a tip from someone who’s been there: don’t skimp on quality to save a few bucks. It’s tempting, but it’ll cost you later. Good steel buildings are built to last, saving you money on repairs and energy bills down the road.
Bottom line? Steel homes can be a smart choice for your bank account. They’re tough, efficient, and can be surprisingly affordable. Just do your homework and budget wisely. Your future self will thank you.
Typical Costs for Standard Home Sizes
Steel homes come in various sizes to fit different needs and budgets. Let’s break down the typical costs for standard home sizes:
Home Size | Square Footage | Cost Range |
---|---|---|
25×40 | 1,000 SF | $50,000 – $145,000 |
30×40 | 1,200 SF | $60,000 – $175,000 |
30×50 | 1,500 SF | $75,000 – $215,000 |
30×60 | 1,800 SF | $90,000 – $260,000 |
40×60 | 2,400 SF | $120,000 – $350,000 |
These prices can vary based on location, materials, and customization. A smaller 25×40 home might be perfect for a bachelor pad or starter home. The 30×40 size could work well for a small family. For those needing more space, the 30×50 or 30×60 options offer room to grow. The largest 40×60 size is ideal for big families or those who love to entertain. Keep in mind, these costs include the basic structure – you’ll need to factor in extras like interior finishes and utilities.
Detailed Costs of Constructing Steel Homes
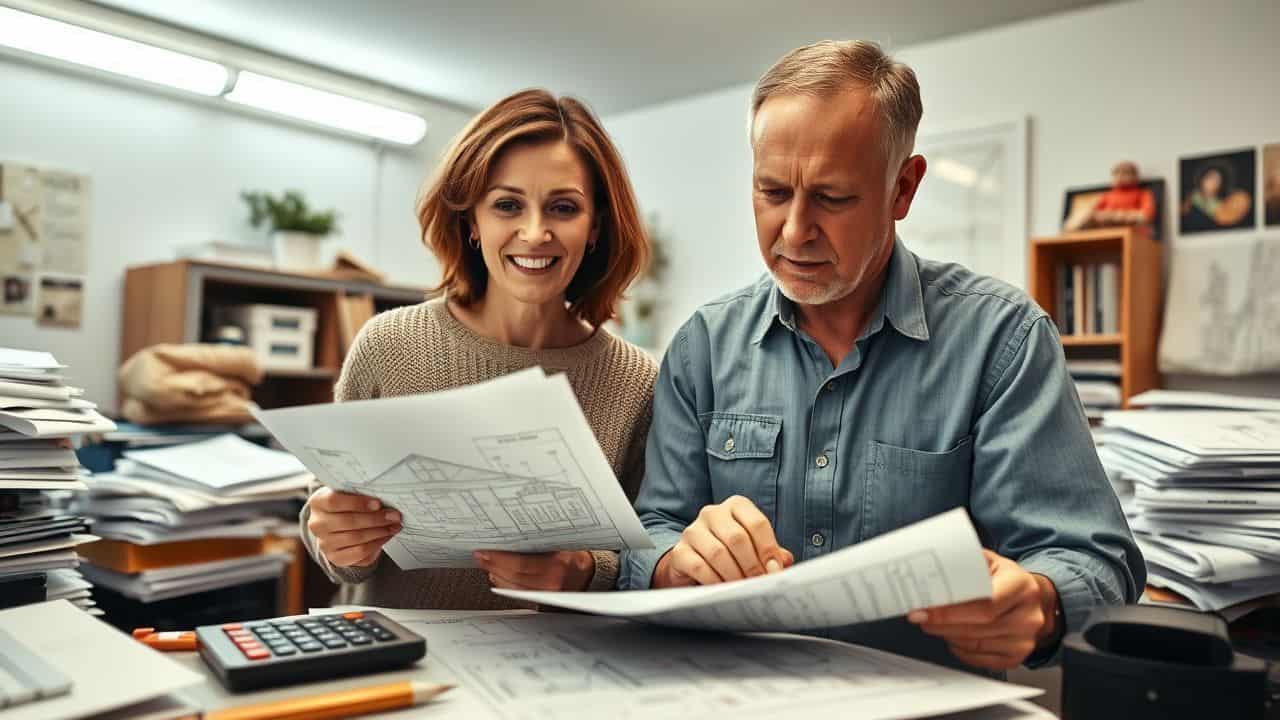
Building a steel home isn’t just about slapping metal sheets together. It’s a mix of big and small costs – from the ground up. Let’s peek at what goes into making these tough houses… and what might hit your wallet.
Foundation and Structural Framing
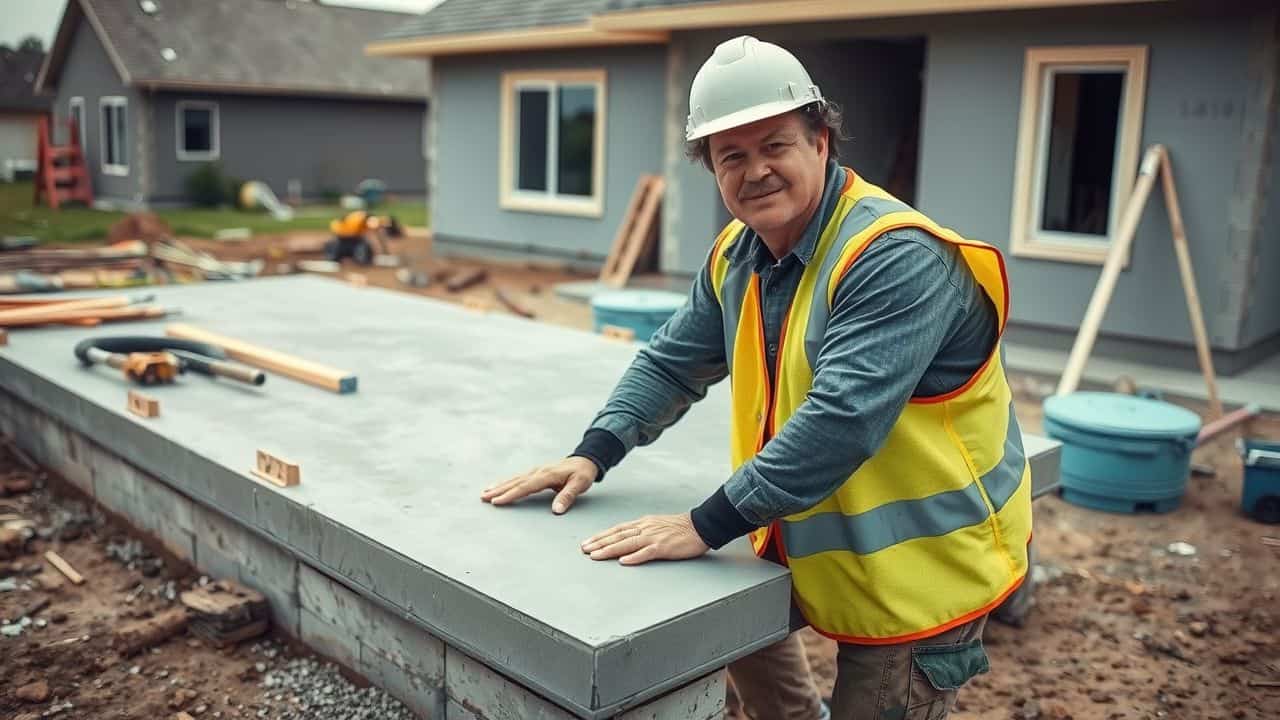
Steel homes start with a solid base. A concrete slab is often the go-to choice, costing $5 to $10 per square foot. This price includes materials and labor. The slab acts as both the foundation and floor, saving you money on separate flooring costs.
Next comes the steel frame – the backbone of your home. It’s tough as nails and won’t rot or warp like wood. The metal building shell runs about $10 to $25 per square foot for materials.
Labor to set it up adds another $5 to $10 per square foot. But don’t sweat it – this frame will stand strong for decades, cutting repair costs down the road.
A steel frame is like a suit of armor for your home – it protects against time, weather, and wear.
Insulation Options and Exterior Siding

After setting up the foundation and framing, it’s time to think about keeping your steel home cozy. Insulation is key here. You’ve got options like spray foam and fiberglass. Spray foam costs more – about $1 to $4.50 per square foot.
But it’s super effective. To get an R-value of R-25, you need 3.5 inches of spray foam. That’ll run you around $3.50 per square foot. Fiberglass is cheaper at $0.50 to $1.50 per square foot.
But it might not work as well in tight spots.
For the outside of your home, you’ve got choices too. Metal siding is popular for steel homes. It’s tough and looks sharp. But don’t rule out other options like vinyl or even wood.
The siding you pick affects how your home looks and how much upkeep it needs. Keep in mind, putting in insulation and siding can be tricky. Labor costs might be more than materials, especially if your home has a complex design.
It’s smart to get quotes from a few contractors to find the best deal.
Interior Finishing and Custom Features
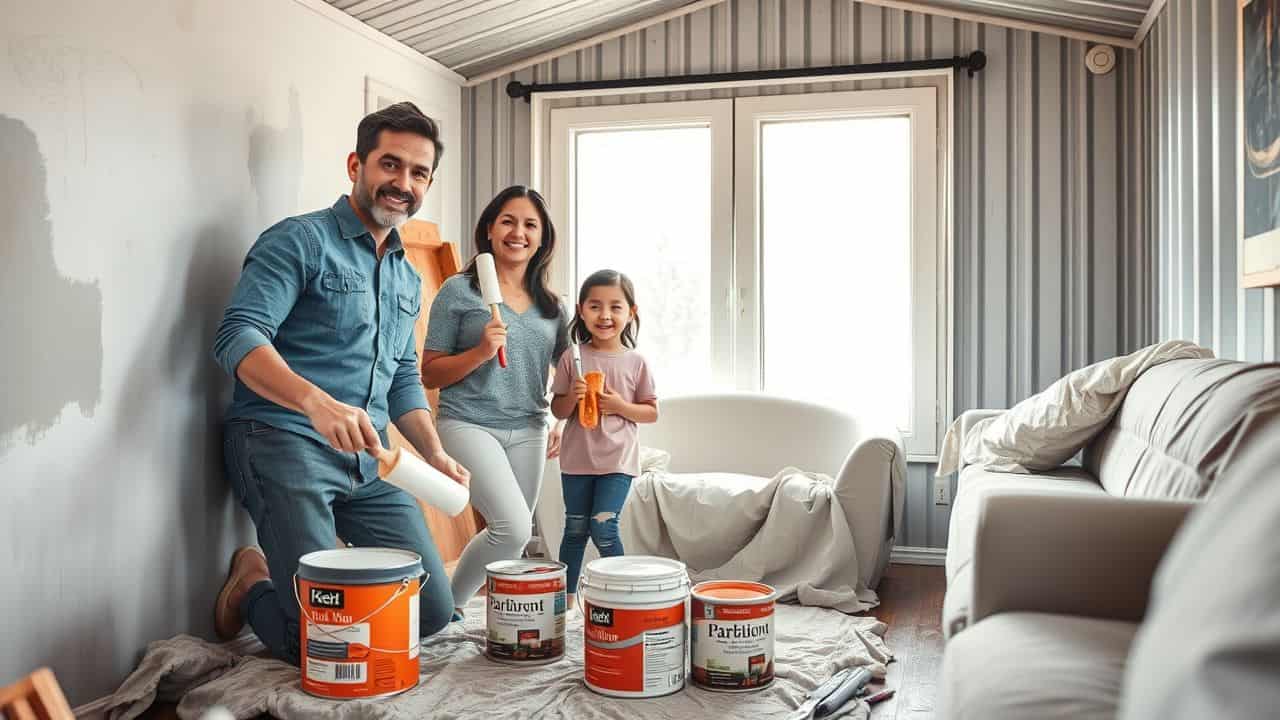
Moving from the outer shell to the inner spaces, let’s talk about making your steel home truly yours. Interior finishing and custom features can turn a basic structure into the home of your dreams.
It’s where you get to flex your creative muscles and add personal touches.
Costs for interior work can vary widely. Painting walls might set you back $1 to $6 per square foot. Kitchen cabinets? They’re a big-ticket item, ranging from $4,500 to $15,000. Don’t forget about HVAC – keeping comfortable ain’t cheap at $7,000 to $16,000.
Overall, expect to shell out $35 to $110 per square foot for interior and exterior finishing. These numbers can make your head spin, but they’re crucial for budgeting. I once helped a buddy with his steel home project.
We saved a bundle by doing some of the painting ourselves. It was hard work, but man, the satisfaction of seeing those walls come to life… priceless!
Comparing Different Types of Steel Homes
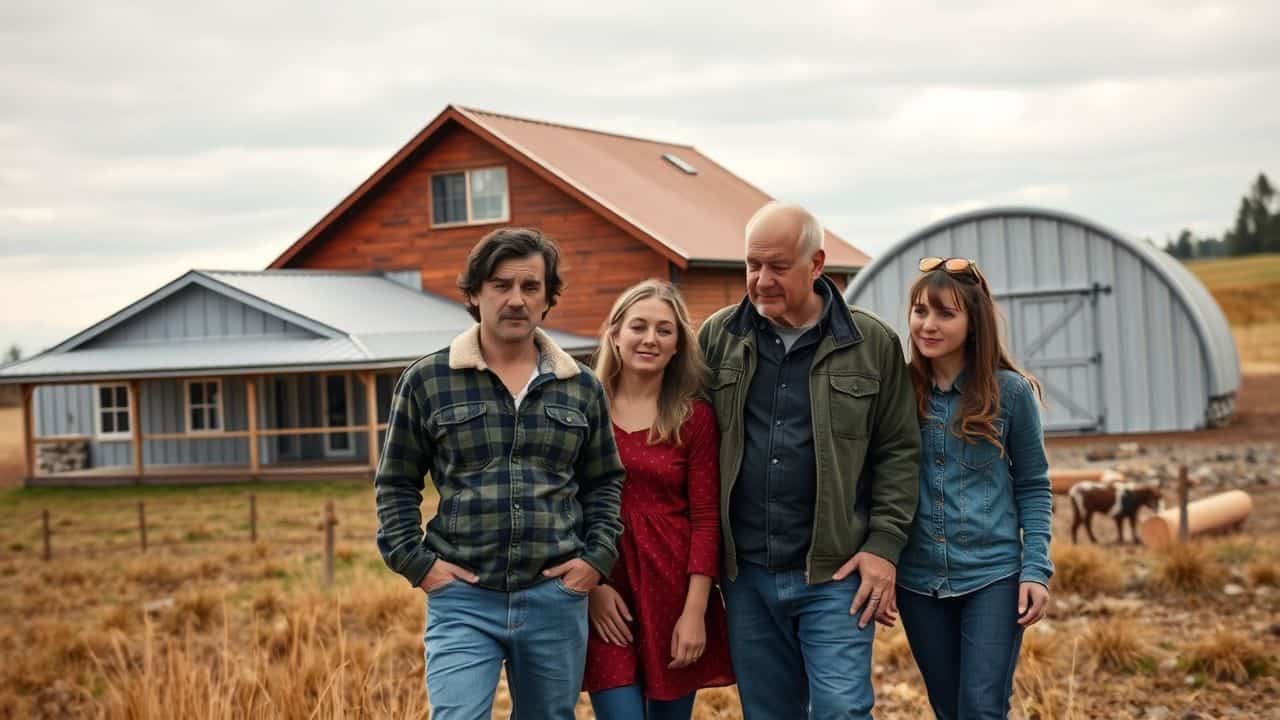
Steel homes come in different shapes and sizes. Let’s look at three popular types: rigid frame, barndominium, and Quonset hut.
Costs of Rigid Frame Structures
Rigid frame structures offer a solid option for steel homes. They’re known for their strength and versatility. Let’s break down the costs:
Cost Component | Price Range (per square foot) |
---|---|
Overall Cost | $45 – $135 |
Shell Materials | $10 – $25 |
Assembly | $5 – $10 |
Finishing | $35 – $110 |
These numbers might make you pause. But no worries, guys. Let’s look at it piece by piece. The shell materials – that’s your basic structure. It’s the bones of your new place. Assembly costs cover getting that shell up and ready. And finishing? That’s where you make it feel like home.
Now, here’s something to think about: A 40×60 metal building home typically costs between $120,000 and $350,000. That’s quite a range, right? It all depends on how much you want to add to your new space.
The costs can change based on where you live, what design you choose, and even when you build. It’s like buying a car – the basic model’s one price, but add extras, and you’re looking at something different.
So, what’s the main point? Rigid frame structures can save you money for your steel home. They’re strong and can be made to fit your style. Just watch those finishing costs – that’s where things can really add up if you’re not paying attention.
Expenses for Barndominium Constructions
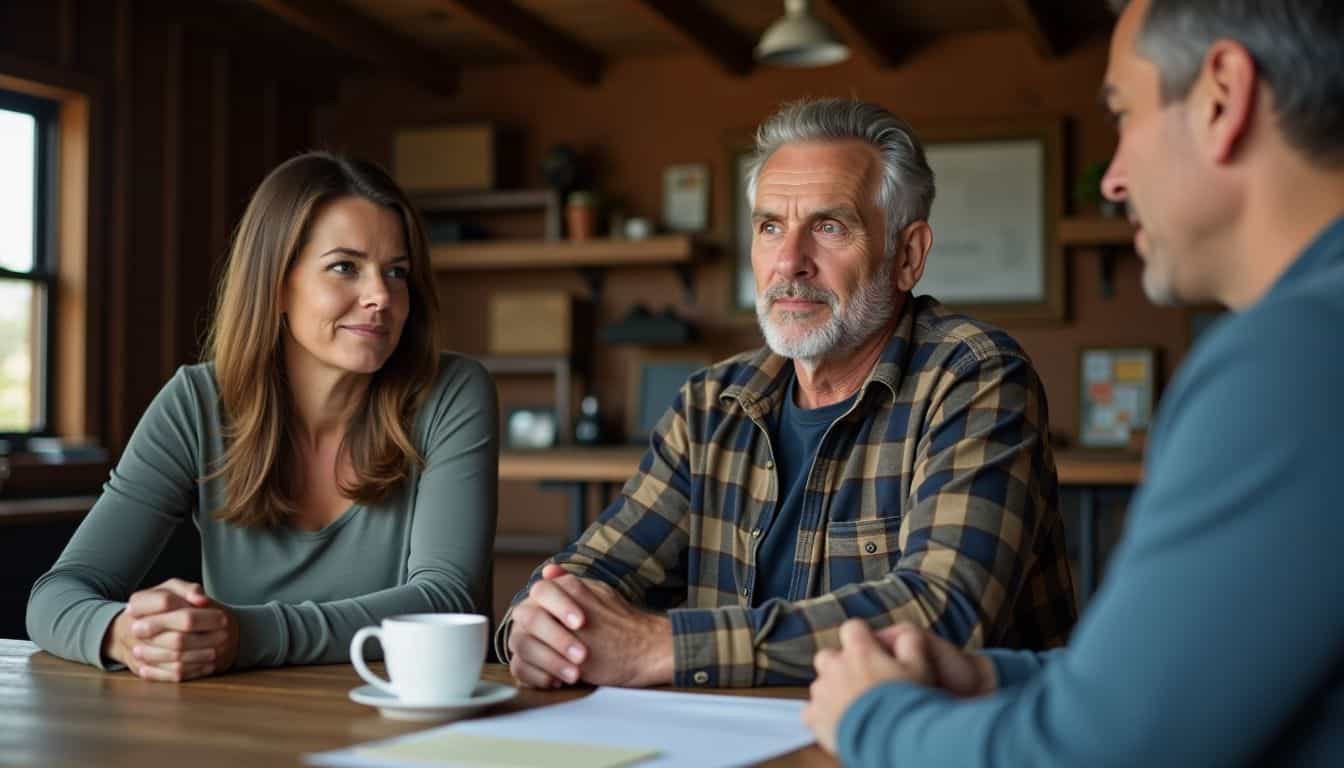
Barndominiums are catching on with DIY fans and cost-conscious homeowners. These metal structures mix rustic appeal with modern living. Here’s a breakdown of the costs:
Cost Component | Price Range | Notes |
---|---|---|
Overall Cost | $65 – $160 per sq ft | Varies based on location and finishes |
Average Total Cost | $150,700 | For a standard-sized barndominium |
Shell Construction | $20 – $40 per sq ft | Includes basic structure and roof |
Interior Finishing | $50 – $120 per sq ft | Depends on quality of materials |
Renovation Costs | Higher than new builds | Due to unforeseen issues in existing structures |
Labor costs for wooden homes are often pricier. Steel structures can save you money in the long run. Now, let’s look at the pricing for Quonset hut installations…
Pricing for Quonset Hut Installations
Quonset huts are making a comeback. These curved metal structures offer a unique blend of affordability and durability. Let’s break down the costs:
Cost Category | Price Range |
---|---|
Kit Package (per sq ft) | $10 – $20 |
Installed Cost (per sq ft) | $17 – $34 |
Construction Labor (per sq ft) | $3 – $6 |
Foundation Installation (per sq ft) | $4 – $8 |
Common hut sizes and their starting prices:
Size | Starting Price |
---|---|
30×40 | $21,816 |
30×60 | $32,724 |
40×60 | $38,784 |
These prices are just the tip of the iceberg. Your final cost depends on factors like location, design complexity, and chosen finishes. But here’s the kicker – Quonset huts often cost less than traditional homes in the long run. They’re tough as nails and need less upkeep. So, while the upfront cost might make you blink, the savings down the road could put a smile on your face.
Key Factors That Affect Steel Home Pricing
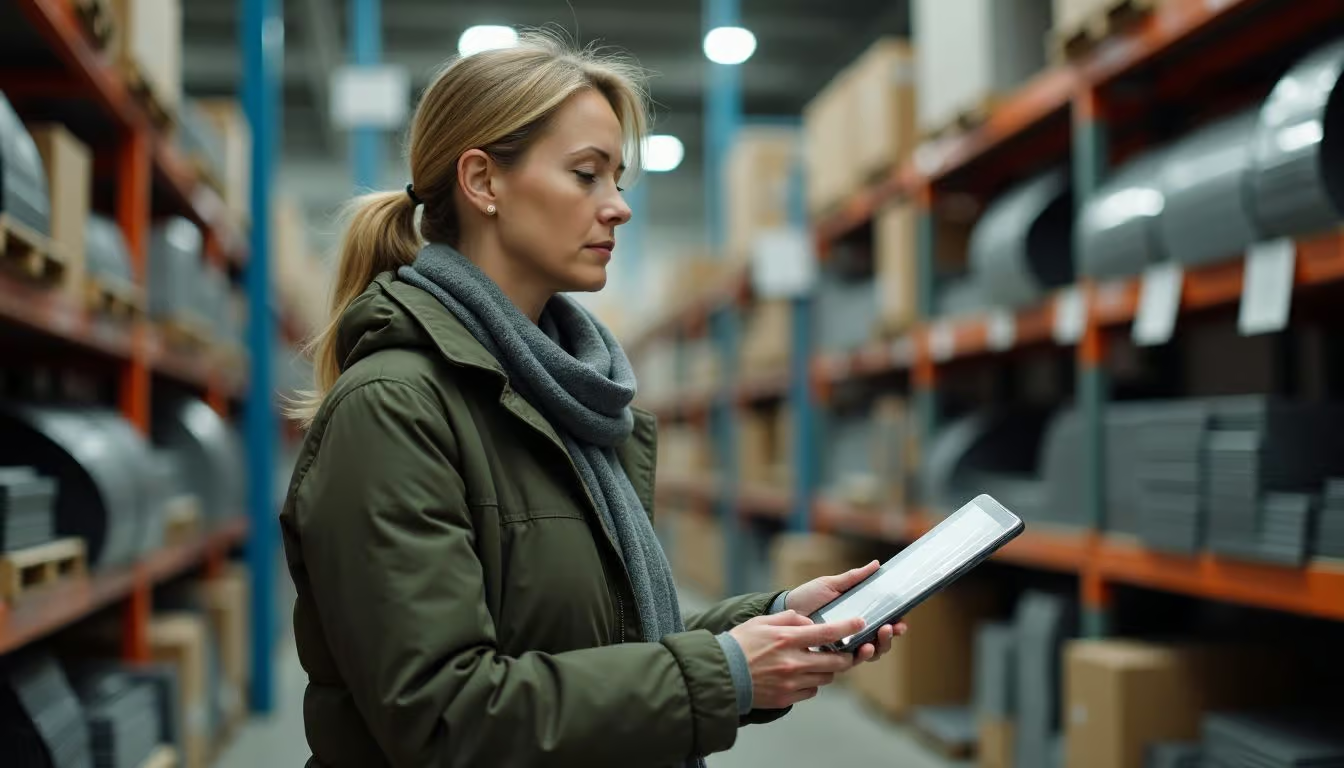
Steel home prices can swing wildly based on size, location, and who you hire. Want to know how to save big bucks? Keep reading….
Impact of Size and Design Complexity
Size matters in steel homes. Bigger homes need more materials, which drives up costs. A small, simple box-shaped house is cheaper than a sprawling mansion with fancy add-ons. Complex designs also hike up prices.
Curved walls, unique roof lines, and custom features require extra work and precision. This means more time and skill from builders, leading to higher labor costs.
In steel homes, every square foot and design twist counts on your wallet.
Fancy doesn’t always mean better, guys. Sometimes, keeping it simple saves big bucks. But don’t worry – you can still get a cool pad without breaking the bank. It’s all about smart choices in size and design.
Next up, we’ll look at how your location can affect the price tag of your steel dream home.
Location and Site Accessibility Effects
Where you build your steel home matters… a lot. Costs can jump if your land is hard to reach or needs extra work. Think about it – if trucks can’t get to your site easily, you’ll pay more for delivery.
And if your plot is on a steep hill or full of rocks, you’ll shell out extra cash for site prep.
Local rules and weather play a big role too. Building codes vary by area and can affect your wallet. Hot or cold climates might need special insulation, upping your costs. Labor rates differ across the country – what’s cheap in one state could break the bank in another.
So, before you pick a spot for your steel dream home, do your homework. It could save you a bundle!
Contractor Selection and Material Costs
Picking the right contractor can make or break your steel home project. Look for pros who are experts in metal buildings. They’ll help you avoid costly mistakes and get excellent results.
Good builders often have connections to quality suppliers, too. This can mean better prices on materials like steel frames and roofing. Don’t just go for the cheapest quote, though.
Quality work is worth it in the long run.
Material costs can change a lot based on market trends. Steel prices can go up and down quickly sometimes. That’s why the timing of your build is important. A good contractor will watch these changes.
They might suggest buying materials when prices are lower. Or they could propose other options if certain items get too expensive. The goal is to balance quality and cost. A good builder will help you make smart choices that fit your budget and needs.
Financial Benefits of Steel Over Traditional Homes
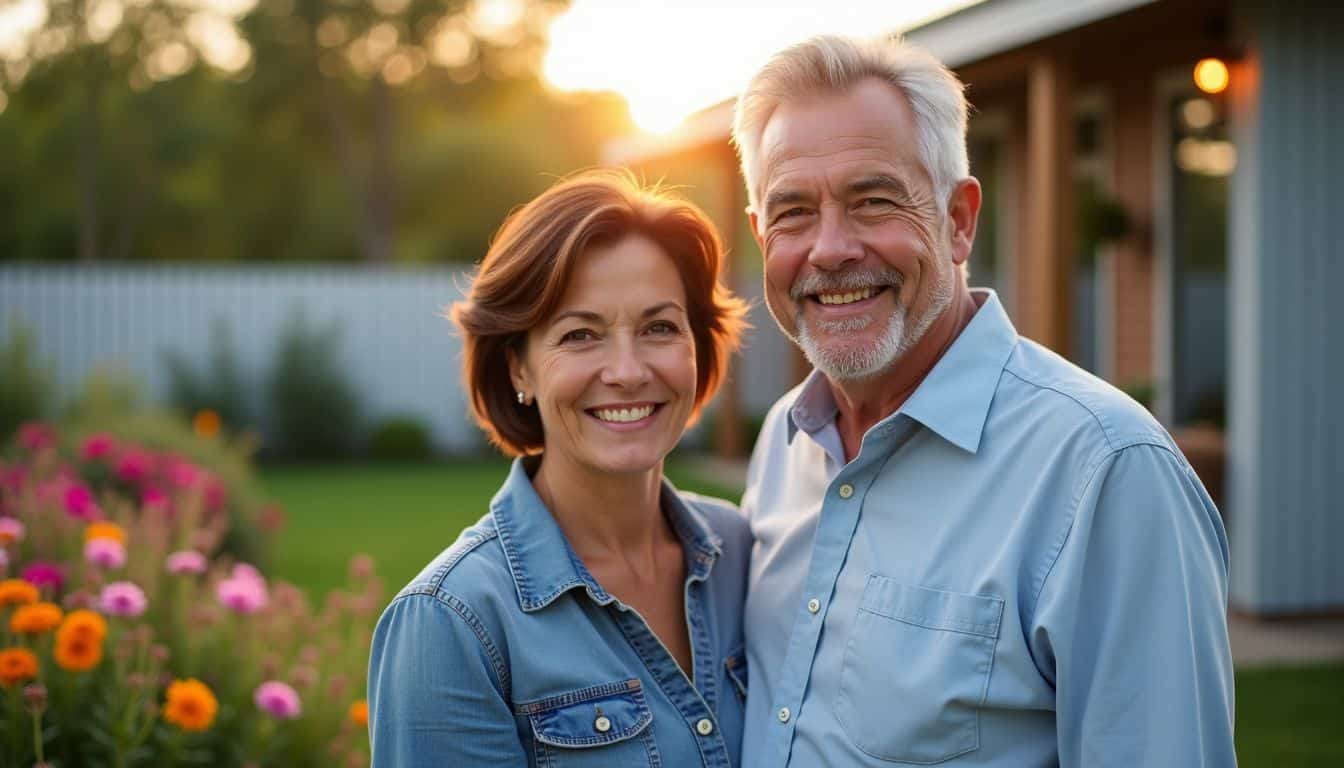
Steel homes can save you big bucks in the long run. They’re tough as nails and need less upkeep than traditional houses – that’s money in your pocket!
Analysis of Long-term Financial Savings
Steel homes pack a punch in saving you money long-term. These tough structures cut utility bills by up to 50% thanks to their energy-efficient design. You’ll spend less on upkeep, too.
Unlike wood, steel doesn’t rot, warp, or attract pests – fewer repairs and replacements down the road. Plus, steel’s strength can lower your insurance costs in areas with harsh weather.
But the savings don’t stop there. Steel homes often come with prefab parts, cutting down on construction time and labor costs. This means you’ll move in faster and start enjoying your new place sooner.
And don’t forget resale value – steel homes tend to hold their worth better over time. So, if you ever decide to sell, you might just pocket a tidy sum.
Comparison of Maintenance Expenses
Moving from long-term savings to day-to-day upkeep, let’s talk about the details of maintenance costs. As guys who like to keep our wallets fat and our stress levels low, this is where steel homes really shine.
Expense Type | Steel Homes | Traditional Homes |
---|---|---|
Annual Maintenance Cost | $1,500 – $2,500 (1% of initial cost) | $7,000 – $20,000 (2-4% of initial cost) |
Pest Control | Minimal to none | Regular treatments needed |
Painting | Every 15–20 years | Every 5–7 years |
Roof Replacement | 50+ years | 20–30 years |
Structural Repairs | Rare | More frequent |
Look at those numbers, fellas. Steel homes are like that trusty old truck that just keeps on truckin’. They need way less babysitting than traditional homes. You’ll save a bundle on pest control – bugs and critters can’t munch on steel. And painting? That’s a once-in-a-blue-moon job with steel.
My buddy Tom got his steel home a while back. He used to spend weekends patching up his old wooden house. Now? He’s out fishing or watching the game. That’s the kind of freedom steel homes give you.
The roof on a steel home is tough as nails. It’ll outlast most of us. And structural repairs? They’re pretty rare. All this adds up to more cash in your pocket and less time wasted on home fix-ups.
Bottom line: Steel homes are low-maintenance champs. They’ll keep your wallet happy and your weekends free. Now that’s what I call a win-win situation.
People Also Ask
Are steel homes cheaper than traditional frame houses?
Steel homes can be a wallet-friendly option. They often cost less than wood-framed houses. The price depends on size, design, and your postal code. But don’t forget, steel is tough as nails and lasts longer. That means fewer repair bills down the road.
What’s the ballpark figure for a steel home?
Hold your horses! Prices vary like crazy. A basic 1,500 sq ft steel home might set you back $150,000 to $250,000. This includes the shell, rooftop, and basic finishes. Remember, costs for HVAC installation, wiring, and a septic system are extra. Always get quotes from different general contractors.
Can I save money on energy bills with a steel home?
You bet! Steel homes are energy-efficient buildings. They keep your hard-earned cash in your pocket. With proper insulation like fiberglass batts or foam, you’ll spend less on heating and cooling. Some folks even see a 50% drop in energy costs. Now that’s something to write home about!
Do steel homes need less upkeep than frame construction?
Absolutely! Steel homes are tough cookies. They laugh in the face of termites and rot. Unlike wood-framed houses, they don’t warp or shrink. This means you’ll shell out less for maintenance over time. It’s like having a superhero house!
Are there any tax breaks for building a steel home?
Good news! Some areas offer tax deductions for energy-efficient buildings. Steel homes often fit the bill. Check with your local tax guru about possible savings. Green building practices might also qualify you for extra perks. It’s like finding money in your couch cushions!
Can I customize a steel home like a traditional house?
You sure can! Steel homes are not one-trick ponies. You can add bedrooms, bathrooms, and even an open concept layout. Want a garage door? No problem. Dreaming of a basement? Go for it! The sky’s the limit with steel. It’s like playing with grown-up Legos!
References
https://homeguide.com/costs/metal-building-homes-cost
https://mavericksteelbuildings.com/steel-homes-vs-traditional-houses-a-value-comparison/
https://steelbuildinginsulation.com/steel-building-insulation-cost/
https://keensbuildings.com/barndominium-cost-vs-house-cost-what-you-need-to-know/
https://www.westernstatesmetalroofing.com/blog/barndominium
https://nationalsteelbuildingscorp.com/2023/11/02/these-8-factors-can-affect-metal-building-pricing/
https://www.eaglecarports.com/blog/metal-building-prices
https://nationalsteelbuildingscorp.com/2023/07/31/6-factors-that-keep-steel-building-costs-reasonable/ (2023-07-31)
https://www.usametalstructures.com/post/financial-benefits-of-metal-buildings-an-in-depth-analysis (2024-08-21)
https://www.summitsteelbuildings.com/20-year-cost-comparison